Maximizing Warehouse Efficiency: 11 Essential Strategies for Success

Last updated on April 02, 2025
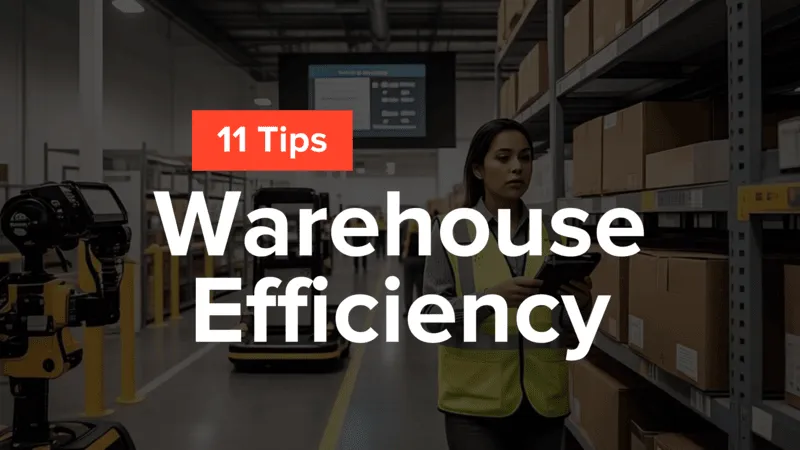
In this article
9 minutes
- How to Measure Warehouse Efficiency
- Optimizing Warehouse Layout and Traffic Flow
- Implementing Advanced Inventory Management Systems for Warehouse Operations
- Adopting Automation and Robotics
- Enhancing Employee Training and Engagement
- Utilizing Data Analytics for Continuous Improvement
- Implementing Lean Inventory Practices
- Enhancing Safety Measures
- Regular Maintenance of Equipment
- Streamlining Communication Channels
- Customizing Storage Solutions
- Conclusion
- Frequently Asked Questions
Efficiency is the backbone of successful warehouse operations. As businesses grow and consumer demands evolve, warehouses must continually refine their processes to stay competitive. Whether it’s optimizing layouts, integrating automation, or enhancing employee training, each improvement contributes to a smoother, faster, and more cost-effective operation. By implementing strategic measures, warehouses can maximize their potential, reduce waste, and improve overall productivity. This article explores a range of strategies to achieve a highly efficient warehouse.
1. How to Measure Warehouse Efficiency
It is absolutely necessary for warehouses to find ways to measure efficiency and identify areas for improvement. Common key performance indicators (KPIs) such as inventory turnover, order cycle time, and perfect order rate can be used to measure warehouse efficiency.
Inventory turnover indicates how often inventory is sold and replaced over a period, reflecting the effectiveness of inventory management, while order cycle time measures the time taken from order placement to delivery, highlighting the speed of warehouse operations. The perfect order rate tracks the percentage of orders delivered without errors.
In addition to those metrics, warehouse managers can use metrics such as storage capacity utilization, labor productivity, and equipment utilization to measure the efficiency of specific aspects of their business. By regularly reviewing these KPIs, warehouse managers can pinpoint inefficiencies and implement targeted improvements to optimize warehouse operations.
2. Optimizing Warehouse Layout and Traffic Flow
A warehouse’s layout can significantly improve or significantly harm efficiency. Optimizing existing warehouse space with a well-designed floor plan can prevent bottlenecks, reduce excessive travel time, and make it easier to locate products. By optimizing warehouse space, businesses can reduce unnecessary movement and streamline workflows.
One effective approach is to position high-demand items closer to packing and shipping areas. This ensures that frequently picked products are easily accessible, reducing the time employees spend retrieving them. Categorizing products based on size and weight also enhances picking speed and accuracy.
Another key consideration is the design of pathways. Wide, clearly marked aisles prevent congestion and allow for the smooth movement of personnel and equipment, such as forklifts and pallet jacks. Regularly reassessing the layout based on inventory trends and operational needs ensures that the warehouse remains adaptable to changes in demand.
3. Implementing Advanced Inventory Management Systems for Warehouse Operations
Managing inventory efficiently is essential for preventing overstocking, stockouts, and misplacement of goods. Advanced inventory management systems (IMS) provide real-time tracking and visibility, helping warehouses maintain optimal stock levels and optimize warehouse efficiency through the use of warehouse management systems (WMS).
Modern IMS solutions incorporate barcode scanning and RFID technology to accurately track inventory movement. These tools reduce human errors, improve order accuracy, and minimize delays caused by misplaced items. Additionally, cloud-based inventory management allows for seamless integration with other business systems, providing instant updates on stock levels, supplier shipments, and order processing.
Automating inventory tracking also enables better demand forecasting. By analyzing historical sales data and market trends, warehouses can anticipate demand fluctuations and adjust inventory levels accordingly. This prevents excess stock from occupying valuable storage space while ensuring that popular products are readily available.
4. Adopting Automation and Robotics
Automation is transforming the warehousing industry by increasing efficiency, accuracy, and speed. Implementing automated solutions reduces reliance on manual labor for repetitive tasks, allowing employees to focus on more complex responsibilities.
Automated guided vehicles (AGVs) and conveyor systems streamline material handling by transporting goods efficiently throughout the warehouse. Robotics, such as automated picking and sorting systems, further enhance productivity by reducing errors and accelerating order fulfillment.
While the initial investment in automation can be significant, the long-term benefits—such as reduced labor costs, increased processing speed, and improved accuracy—justify the expense. Additionally, integrating warehouse management systems (WMS) with automation ensures seamless coordination between various operational processes, further optimizing efficiency.
5. Enhancing Employee Training and Engagement
Even with advanced technology, human employees remain (and will remain) a crucial element of a well-managed warehouse operation. Well-trained and motivated staff contribute significantly to streamlined operations and improved accuracy. Regular training programs ensure that employees are proficient in using warehouse technology, safety protocols, and best practices.
Engagement is equally important. Incentivizing employees with performance-based rewards encourages efficiency and accuracy. Open communication channels, feedback mechanisms, and a positive work environment foster a sense of ownership among workers, increasing productivity and reducing turnover rates.
6. Utilizing Data Analytics for Continuous Improvement
Data-driven decision-making is a powerful tool for warehouse optimization. By analyzing key performance indicators (KPIs) and evaluating and streamlining warehouse processes, businesses can identify inefficiencies and make informed improvements.
Metrics such as order accuracy rates, picking and packing times, and inventory turnover ratios provide insights into operational strengths and weaknesses. Predictive analytics can also enhance efficiency by anticipating demand patterns, optimizing workforce allocation, and minimizing waste. By leveraging data analytics, warehouses can continuously refine their processes and maintain a competitive edge.
Looking for a New 3PL? Start with this Free RFP Template
Cut weeks off your selection process. Avoid pitfalls. Get the only 3PL RFP checklist built for ecommerce brands, absolutely free.
Get My Free 3PL RFP7. Implementing Lean Inventory Practices
Adopting lean inventory management principles helps minimize waste and maximize resource utilization. The Just-in-Time (JIT) inventory system is a popular lean approach that ensures stock arrives only when needed, reducing storage costs and excess inventory. Implementing JIT requires strong supplier relationships and precise demand forecasting to avoid stockouts.
Lean inventory practices emphasize efficiency in every aspect of warehouse management, from procurement to fulfillment. By maintaining optimal stock levels and eliminating unnecessary storage, warehouses can reduce costs while improving service levels.
8. Enhancing Safety Measures
A safe warehouse is an efficient warehouse. Aside from their toll on personal health, workplace injuries and accidents lead to downtime, decreased productivity, and increased operational costs. Prioritizing safety measures ensures a secure working environment and smooth operations.
Regular safety training, clear signage, and well-maintained equipment help prevent accidents. Implementing ergonomic workstations reduces strain-related injuries among employees. Additionally, enforcing proper safety protocols for operating machinery, handling hazardous materials, and lifting heavy objects minimizes risks.
Investing in safety not only protects employees but also enhances overall efficiency by preventing disruptions caused by workplace incidents. A culture of safety encourages employees to adhere to best practices, creating a more productive work environment.
9. Regular Maintenance of Equipment
Warehouse equipment plays a vital role in daily operations, and its reliability is crucial for efficiency. Regular maintenance prevents unexpected breakdowns that can disrupt workflows and delay order fulfillment.
A preventive maintenance program ensures that forklifts, conveyor belts, and other machinery remain in optimal working condition. Scheduling routine inspections, replacing worn-out components, and addressing minor issues before they escalate prolong the lifespan of equipment and reduce downtime.
Additionally, maintaining accurate records of maintenance activities allows managers to track equipment performance and plan for necessary upgrades or replacements. A proactive approach to maintenance keeps warehouse operations running smoothly and efficiently.
10. Streamlining Communication Channels
Effective communication is the backbone of a well-coordinated warehouse. Miscommunication can lead to errors, delays, and inefficiencies, making it essential to establish clear communication channels between employees and departments.
Implementing communication tools such as warehouse management software (WMS) with real-time messaging features enhances coordination. Regular team meetings ensure that staff are aligned on operational goals, workflow changes, and performance expectations.
Encouraging an open-door policy where employees can voice concerns and suggest improvements fosters collaboration and innovation. By maintaining clear and transparent communication, warehouses can minimize misunderstandings and enhance overall productivity.
Scaling Made Easy: Calis Books’ Fulfillment Journey
Learn how Calis Books expanded nationwide, reduced errors, grew sales while cutting headcount, and saved BIG with Cahoot
See Scale Journey11. Customizing Storage Solutions
Optimizing storage systems improves space utilization and accessibility, leading to more efficient warehouse operations. Customizable storage solutions cater to the specific needs of different products, enhancing organization and retrieval speed.
Adjustable shelving, modular racking, and vertical storage units maximize available space while ensuring easy access to items. Implementing clear labeling systems further streamlines picking and stocking processes. In addition, regularly assessing storage requirements and reconfiguring layouts based on inventory trends helps warehouses maintain efficiency. Customizing storage solutions to fit the business’s needs prevents wasted space and enhances operational flow.
Conclusion
Improving warehouse efficiency requires a combination of strategic planning, technological integration, and workforce optimization. By continuously evaluating and refining processes, warehouses can achieve greater productivity, reduce costs, and enhance customer satisfaction. The key to success lies in embracing innovation, fostering a culture of efficiency, and staying adaptable to industry changes. With a commitment to continuous improvement, warehouses can position themselves as leaders in operational excellence.
Frequently Asked Questions
What are some cost-effective ways small warehouses can improve efficiency without investing in expensive automation?
Small warehouses can enhance efficiency by optimizing their layout to reduce unnecessary movement, implementing lean inventory practices to minimize waste, and utilizing affordable inventory management software to track stock levels more accurately. Training employees to follow standardized workflows and adopting basic automation tools, such as barcode scanners, can also help improve speed and accuracy. Additionally, regularly analyzing key performance metrics can help small warehouses identify inefficiencies and make strategic improvements without requiring a large financial investment.
What are the biggest challenges warehouses face when trying to implement new efficiency strategies?
One of the most common challenges is employee resistance to change, as new processes or technology may require additional training and adaptation. High upfront costs for automation and technology upgrades can also be a barrier, especially for smaller operations. Furthermore, integrating new systems with existing workflows can be complex and time-consuming, potentially causing temporary disruptions. To overcome these obstacles, warehouses should prioritize phased implementation, provide comprehensive training, and ensure clear communication about the benefits of the changes to gain employee buy-in.
What strategies can warehouses use to manage seasonal demand fluctuations?
Seasonal demand can create significant operational challenges, including stock shortages, overstocking, and increased labor costs due to fluctuating order volumes. Warehouses can prepare by analyzing historical sales data to anticipate demand spikes and adjust inventory levels accordingly. Implementing flexible storage solutions, such as temporary shelving or rented warehouse space, can help accommodate excess stock when needed. Additionally, hiring temporary workers and cross-training existing employees can ensure that labor capacity aligns with seasonal surges, preventing bottlenecks and maintaining order fulfillment efficiency.
How can warehouses incorporate sustainability into their efficiency strategies, and what are the benefits?
Warehouses can improve efficiency while promoting sustainability by adopting energy-efficient lighting, optimizing transportation routes to reduce fuel consumption, and using eco-friendly packaging materials. Implementing waste reduction strategies, such as recycling programs and reusable packaging, can further enhance environmental responsibility. Not only do these practices help reduce operational costs, but they also improve a company’s reputation and align with increasing consumer demand for sustainable business practices. By integrating sustainability into warehouse operations, businesses can create long-term cost savings while contributing to a greener supply chain.
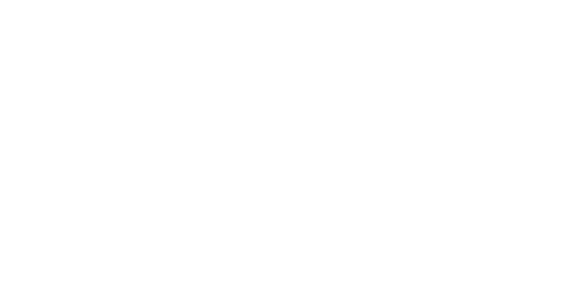
Turn Returns Into New Revenue
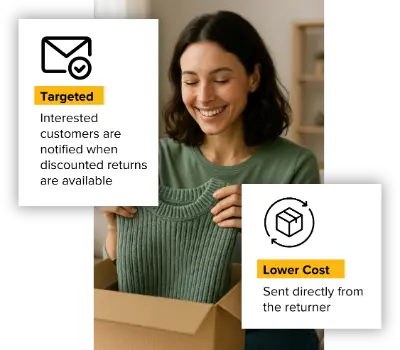