Warehouse Picking Process: Pick and Pack Fulfillment – An Ecommerce Guide | Cahoot

Last updated on February 12, 2025
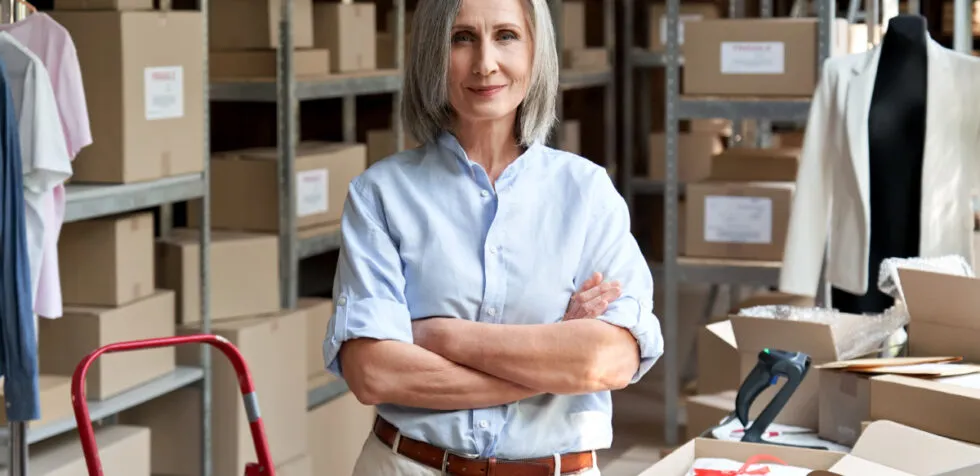
In this article
16 minutes
- What is Warehouse Picking?
- Why Pick and Pack Fulfillment Quality Matters for Customer Satisfaction
- Pick and Pack Warehouse Picking Strategies
- Technology in Warehouse Picking
- Warehouse Order Picking Best Practices
- Common Challenges in Warehouse Picking
- How Does Pick and Pack Work for Fragile Items?
- Future Trends in Warehouse Picking
- Cahoot: The Best Pick and Pack Fulfillment Service
- Frequently Asked Questions
Simply put, “pick and pack” is the process of picking a customer’s order off of a shelf (or wherever it’s stored) and packing it in a box to be shipped to the customer. If you’re a new seller with just a few orders a day, you’re probably doing your own picking and packing – maybe out of your living room! The time, energy, and focus it takes to correctly pick and pack order after order quickly overwhelms sellers as they grow, though, which is why most turn to a 3PL and outsource their ecommerce order fulfillment once they get traction in the market. As you can imagine, picking and packing gets a lot more complex in a warehouse optimized for speedy and accurate ecommerce fulfillment. Read on to learn how pick and pack quality impacts your ecommerce store, how the experts optimize their order picking, and how you can find the best pick and pack fulfillment service for your needs.
What is Warehouse Picking?
Warehouse picking is the process of selecting and retrieving products from a warehouse or storage facility to fulfill customer orders. It is a critical component of the supply chain and plays a vital role in ensuring customer satisfaction. The picking process involves several steps, starting with receiving products into the warehouse, storing them in designated locations, and then picking the items as orders come in. Strategic planning, coordination, and execution are essential to ensure efficiency and accuracy in warehouse picking. By optimizing these processes, businesses can improve their overall operational efficiency and deliver a better experience to their customers.
Why Pick and Pack Fulfillment Quality Matters for Customer Satisfaction
Picking speed is an essential behind-the-scenes metric for ecommerce stores because it dictates order cutoffs and on-time delivery. These metrics in turn have a big impact on your conversion rate and repeat customer rate, and therefore your overall growth!
Your order cutoff time is the time in the day before which a customer has to place an order that can be shipped out that same day. Faster, more efficient picking operations can set later order cutoffs. In the days of 7 day shipping, this wasn’t such a big deal. With the rise of 1 and 2-day shipping, though, missing an order cutoff means a customer has to wait twice as long to receive their package. According to McKinsey, almost half of online shoppers will buy elsewhere when the estimated delivery time is too long – so an early cutoff means lost customers.
Picking accuracy is perhaps even more important than picking speed. As more sellers pile into ecommerce, price and advertising competition continue to rise, squeezing margins. Repeat customers who don’t need advertising to convert are critical to a seller’s ability to build a sustainable long-term business model. Sending customers the wrong order kills a brand’s image, likely loses the chance to create a long-term customer, and on top of that incurs return shipping fees.
Finally, intelligent packing can make the difference between a profitable sale and an unprofitable one. How? It’s all in the box.
It’s easy enough to set rules that guide which single item orders are put in which boxes. But what about multi-item or multi-quantity orders? They can quickly get confusing for warehouse personnel, and workers under pressure to go fast default to using too-big boxes to fit all the items. That, in turn, increases the dimensional weight of the box, which increases the cost of the shipping label.
Top ecommerce fulfillment 3PLs like Cahoot have efficient picking operations that work quickly while minimizing errors and cost. Cahoot’s processes enable 2 pm cutoff times that are a full two hours later than the industry standard, while its teams use barcode scanners to eliminate errors. When every single pick is checked by a computer, the order is right every time. Finally, Cahoot software creates intelligent and dynamic rules even for the most complicated multi-item orders that minimize shipping cost, saving you money.
Slash Your Fulfillment Costs by Up to 30%
Cut shipping expenses by 30% and boost profit with Cahoot's AI-optimized fulfillment services and modern tech —no overheads and no humans required!
I'm Interested in Saving Time and MoneyPick and Pack Warehouse Picking Strategies
How does picking and packing work in an ecommerce warehouse? The answer varies widely based on the sophistication of the operation and what types of items they’re working with. Automation also has a huge impact on how warehouses pick and pack, with the most tech-forward operations leaning heavily on robots and conveyor belts to quickly move items to humans doing the picking and packing. Different warehouse picking strategies can be employed to optimize efficiency and accuracy, depending on the specific needs of the operation.
Piece Pick and Pack
Piece Picking is the most straightforward method. Fulfillment personnel will pick orders one at a time as they come in, moving about the warehouse to pick items before returning to a packing station to prep the package for handoff to a carrier.
In most warehouses, each item will be stored in its own bin or case in a distinct location. When an order comes in, warehouse software will automatically generate a “pick list” that tells the worker where each item is stored in the warehouse. That way, the worker knows where to go to find each item and can grab them one at a time.
While this is the simplest pick and pack method, it’s also the least efficient, and most medium-to-large warehouses have moved past it.
Batch pick and pack
Batch Picking is similar to Piece Picking in that workers still move about the warehouse picking items for individual orders, but in Batch Picking, workers pick items to fulfill more than one order at a time.
Intelligent warehouse management software (WMS) guides this process to its optimal level of efficiency. Larger warehouses with more orders coming in have more opportunities for personnel to pick for multiple orders at once. Let’s say that four orders come in for the same pack of soap within three minutes of one another; in this simple example, the WMS will send just one worker to pick the soap for all four orders, bring it all back to a packing station, and to pack all the orders sequentially. Of course, this saves several trips to the soap shelf and helps the warehouse run more efficiently.
Zone pick and pack
Zone Picking is the first big step up in complexity, and it involves splitting the entire warehouse into different “zones” and giving different workers responsibility for each zone. Order pickers stay in their zone, and they pick items from their assigned zone only. Instead of the worker passing from zone to zone, they pass the picking box or cart over to the next zone from which it needs items. Once all of the needed items have been picked, they’re passed to the packing station, which is a separate and final zone.
Warehouses that use Zone Picking often have automated parts of the process – for instance, many will have conveyor belts that connect different zones to one another. That makes handoffs between personnel in different zones much quicker and more efficient, freeing them up to focus on fast and accurate picking. Each zone will also connect to the packing station via conveyor belt, so that orders of single units can quickly be passed up to the packing station for shipping.
Wave pick and pack
Finally, Wave Picking combines Zone Picking and Batch Picking. Each zone picks a large amount of items needed for orders in a batch, and then that batch is combined with batches from each other zone and sent up to the packing station. Workers at the packing station then grab what they need for orders from the batches packed from each zone to prepare for shipping.
Like Zone Picking, Wave Picking benefits significantly from automation and is frequently employed in large, sophisticated ecommerce fulfillment facilities.
Technology in Warehouse Picking
Technology plays a vital role in enhancing warehouse picking processes. Some of the most common technologies used in warehouse picking include:
- Warehouse Management Systems (WMS): A WMS is a software solution that manages and optimizes warehouse operations, including picking, packing, and shipping. It helps streamline the entire picking process by providing real-time data and insights, ensuring that orders are fulfilled accurately and efficiently.
- Voice Picking: Voice picking uses voice commands to guide pickers through the picking process. This hands-free technology improves accuracy and efficiency by allowing pickers to focus on their tasks without the need to handle paper lists or devices. Voice-directed picking with natural language processing moves beyond simple voice commands to systems that understand more complex natural language, reducing errors and training time.
- Collaborative Mobile Robots (Cobots): Employing collaborative robots (cobots) that can safely work alongside human pickers in shared workspaces, performing tasks like transporting picked items or assisting with heavy lifting. These robots are designed to work alongside human pickers, handling repetitive and labor-intensive tasks, enhancing productivity and reducing the physical strain on workers.
- Barcode Scanning: Barcode scanning, (a.k.a. Pick Scanning), uses barcodes to track and verify products throughout the picking process. This technology improves accuracy by ensuring that the correct items are picked and reduces the likelihood of errors leading to re-picks (which also reduces the likelihood of working putting the mis-pick back in the wrong bin location).
- Automated Guided Vehicles (AGVs): AGVs are robotic vehicles that automate the transportation of products within the warehouse. They improve efficiency by reducing the time and labor required to move items from one location to another, allowing human workers to focus on more complex tasks.
Warehouse Order Picking Best Practices
Implementing best practices in warehouse order picking can help improve efficiency, accuracy, and customer satisfaction, while limiting the amount of financial waste. Some of the most effective best practices include:
- Optimizing Warehouse Layout: A well-organized warehouse layout can significantly reduce travel time for pickers, improving overall picking efficiency. Grouping frequently picked items together and placing them in easily accessible locations can streamline the picking process.
- Implementing Efficient Picking Methods: Utilizing efficient picking methods, such as Batch Picking or Zone Picking, can enhance productivity and reduce labor costs. These methods allow pickers to handle many orders simultaneously or focus on specific zones, minimizing unnecessary movement. Personalized picking instructions based on worker experience tailors picking workflows to individual worker experience levels, optimizing for both speed and accuracy.
- Utilizing Technology: Leveraging technology, such as WMS or VoicePicking, can improve accuracy and efficiency in the picking process. These tools provide real-time data and guidance, helping pickers make informed decisions and reducing the likelihood of errors. Using computer vision to identify items during picking is another technology that reduces errors and speeds up verification.
- Providing Continuous Training: Continuous training for pickers is essential to maintain high levels of accuracy and efficiency. Regular training sessions can help workers stay updated on best practices, new technologies, and safety protocols, reducing errors and improving overall performance.
Looking for a New 3PL? Start with this Free RFP Template
Cut weeks off your selection process. Avoid pitfalls. Get the only 3PL RFP checklist built for ecommerce brands, absolutely free.
Get My Free 3PL RFPCommon Challenges in Warehouse Picking
Warehouse picking is a complex process that presents several challenges, including:
- Inaccurate Inventory: Inaccurate inventory records can lead to picking errors, delays, and lost sales. Ensuring accurate inventory management is crucial to avoid these issues and maintain efficient warehouse operations.
- Inefficient Picking Routes: Inefficient picking routes can cause pickers to travel long distances within the warehouse, leading to longer pick times and higher labor costs. Optimizing picking routes through strategic planning and technology can help reduce travel time which improves efficiency.
- Labor-Intensive Processes: Manual picking processes can be labor-intensive, leading to higher labor costs and potential errors. Automating repetitive tasks and utilizing technology can help reduce the physical strain on workers and improve accuracy.
- Lack of Training: Untrained or poorly trained staff can lead to mistakes, inefficiencies, and safety risks. Providing comprehensive training and ongoing education for warehouse staff is essential to ensure smooth and accurate picking processes.
- Compliance and Regulations: Warehouses must comply with various industry regulations and standards, which can be challenging to manage. Staying updated on regulatory requirements and implementing compliance measures is crucial to avoid penalties and maintain operational efficiency.
How Does Pick and Pack Work for Fragile Items?
When picking and packing fragile items, speed becomes less important than the safety of the goods. After all, sending items that arrive broken is even worse than sending items slowly; you’ll have to write off the value of the broken items and pay to ship out replacements.
Picking and packing fragile items so that they don’t break in the warehouse or during transit used to come down to the experience and know-how of individual staff. Like most processes in the warehouse, though, guesswork is being replaced by intelligent automated rules to ensure that products arrive safely.
Consider our example below of a host of fragile goods from a fine Italian food purveyor. Each item is a damage risk, making an order with all of them a nightmare for most warehouse personnel.
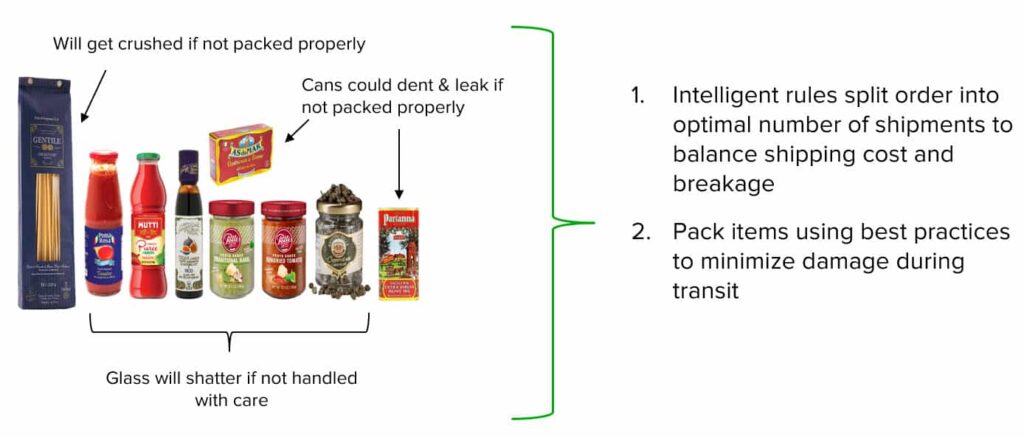
An intelligent shipping software will make the difficult feasible by splitting the order into a number of shipments that finely balances shipping cost and breakage risk. It will then give guidance to the packing station on how to precisely protect and package each item to fit into the smallest box that will prevent damage in transit.
Many warehouses are set up for peak speed and efficiency, and thus, they don’t have the flexibility to intelligently adapt to different types of goods that need different treatment. That’s where Cahoot sets itself apart.
Future Trends in Warehouse Picking
The world of warehouse picking is constantly evolving, driven by technological advancements, changing consumer demands, and global economic shifts. Some of the future trends in warehouse picking include:
- Adoption of Artificial Intelligence: Artificial intelligence is expected to play a larger role in warehouse picking, automating tasks, and improving efficiency. AI-powered systems can analyze data, dynamically calculate the most efficient picking routes in real-time, considering factors like traffic, order priority, and worker location, and predict demand, enhancing overall warehouse operations.
- Increased Use of Robotics: Robotics is expected to become more prevalent in warehouse picking, automating tasks, and improving efficiency. Advanced robots can handle complex picking tasks, work alongside human workers, and adapt to changing warehouse environments.
- Growing Importance of Sustainability: Sustainability is becoming increasingly important in warehouse picking, with companies looking for ways to reduce their environmental impact. Implementing eco-friendly practices such as reducing waste and optimizing energy use can help warehouses become more sustainable.
- Blockchain for supply chain transparency and tracking: Using blockchain technology to track items throughout the supply chain with up to the minute status and location.
- Increased Focus on Customer Satisfaction: Customer satisfaction is becoming increasingly important in warehouse picking, with companies looking for ways to improve delivery times and fulfillment accuracy. Enhancing the picking process through technology and best practices can help meet customer expectations and drive business growth.
By staying ahead of these trends and continuously improving their picking processes, warehouses can ensure they remain competitive and meet the evolving needs of their customers.
Scaling Made Easy: Calis Books’ Fulfillment Journey
Learn how Calis Books expanded nationwide, reduced errors, grew sales while cutting headcount, and saved BIG with Cahoot
See Scale JourneyCahoot: The Best Pick and Pack Fulfillment Service
Cahoot’s nationwide network of over 100 warehouses provides affordable national ecommerce order fulfillment for online merchants. Our wide and diverse network enables us to fulfill a wide variety of needs, from sellers who need absolute peak speed at minimum cost to those that have fragile items or others that require special handling.
Our fulfillment centers are outfitted with dedicated personnel and technology that confers all the benefits of a top pick and pack service:
- Efficient picking enables late (2pm local time) order cutoffs
- Barcode scanning all but eliminates fulfillment defects
- Intelligent pick and pack software optimizes box size for every order, minimizing shipping cost for simple and complex orders
- Lowest cost by design
Unlike other providers, Cahoot also has the flexibility to work alongside existing merchant-owned warehouses (if you have them). We know that many merchants with non-standard items and order profiles carefully manage fulfillment themselves due to how difficult the process can be. Cahoot will analyze your existing network and customer base, then add a few locations of our own to seamlessly extend your network into a nationwide footprint.
With this approach, you can continue to get value out of your existing assets while delighting your customers and your bottom line with affordable fast shipping. Of course, our approach works just as well for merchants who want to fully outsource their fulfillment, and we’d be more than happy to take that on. Getting started with Cahoot is fast and easy – with pre-built integrations for major ecommerce channels like Amazon, Walmart, Shopify, and BigCommerce, we can get merchants started in as little time as it takes to send us your inventory. Talk to one of our experts today and explore how we can be the key that unlocks the next level of your profitable ecommerce growth.
Frequently Asked Questions
What is warehouse picking?
Warehouse picking is an order fulfillment process where item(s) from a customer order are retrieved from their inventory location(s) in a fulfillment or distribution center such as in a bin or on a shelf or pallet. Warehouse picking is the step that occurs before products are packaged and shipped out to their destination.
What is the picking process in a warehouse?
Warehouse picking is the process of finding items within a warehouse or fulfillment center and preparing them for shipment to customers. But there’s a lot of different ways to go about warehouse picking to ensure that it’s done as effectively and efficiently as possible.
What do you do as a warehouse picker?
Warehouse pickers are responsible for finding, picking, and packing goods for dispatch. They work in various locations, including e-commerce warehouses, wholesalers, and cold storage warehouses. It’s a physically demanding role that involves bending, lifting, and carrying products.
How to do picking in warehouses?
There are many strategies for picking in warehouses, which include batch picking, wave picking, zone picking, and piece picking. The best strategy for your warehouse picking setup will depend on the order volume running through your warehouse, the total number of SKUs in storage, your total number of pickers working at the same time, the type of facility you have, and the inventory management system and other technologies you have at your disposal. The different picking methods each have their own advantages and drawbacks.
What is voice picking in a warehouse?
Voice picking is a method of warehouse picking where pickers are equipped with a headset and microphone so they can easily communicate with the warehouse manager about picking details. Some systems are connected with an automated management system, which eliminates the need for a human on the other end of the line. Similar to other wearable warehouse picking options, voice picking has proven to be a time-efficient method and it also cuts down the likelihood of picking errors.
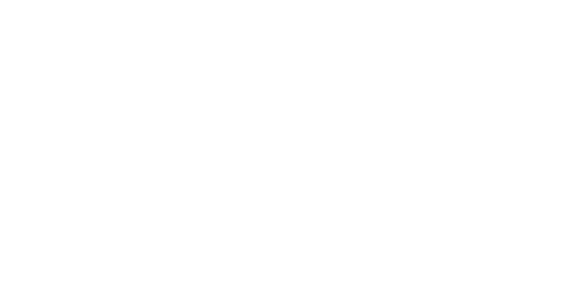
Turn Returns Into New Revenue
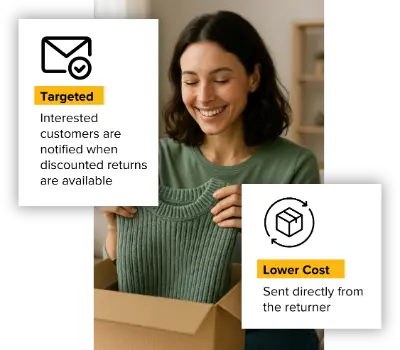